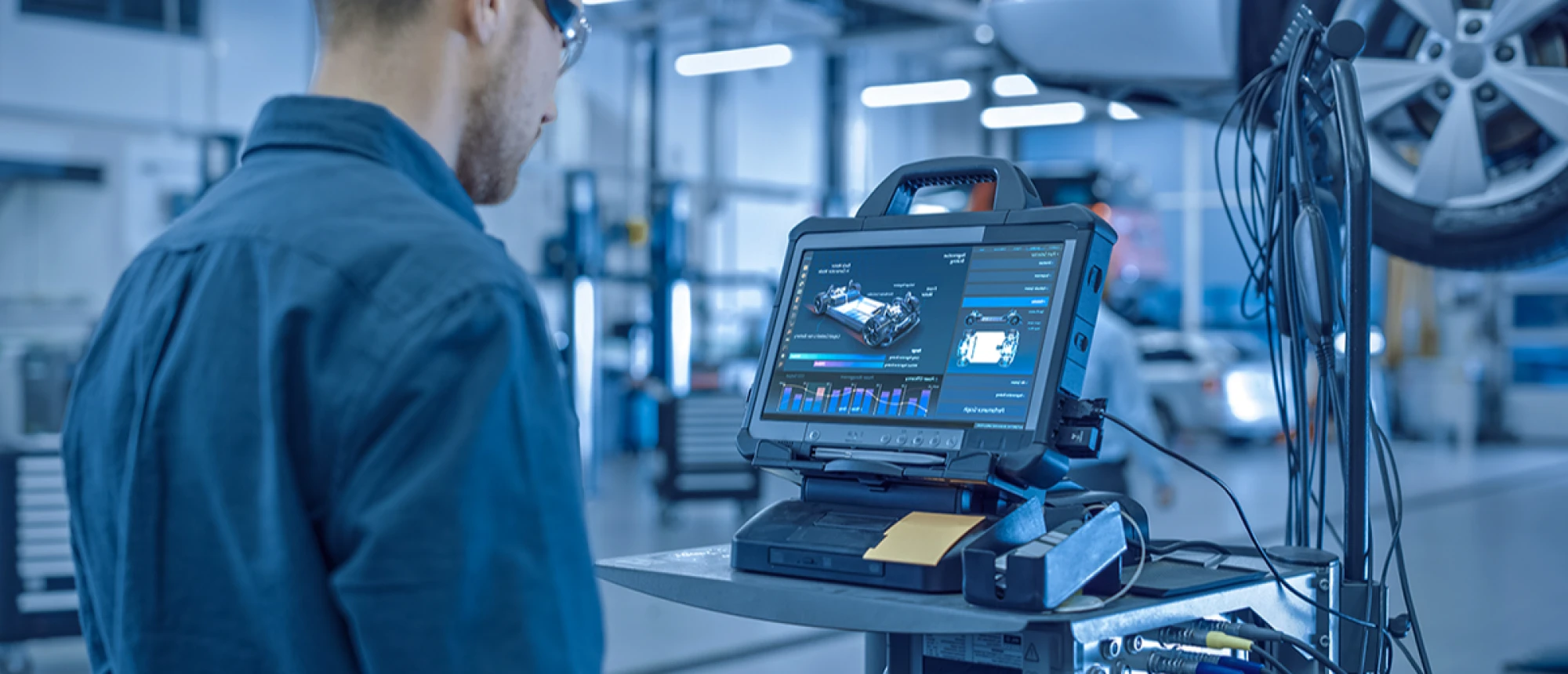
Technical
Retrofit, Reflash & WIP Reduction
Our internationally acclaimed retrofit, reflash and WIP reduction service sees experienced technicians deployed to inspect suspect finished products and perform remedial actions where non-conformances are identified. The data from these activities facilitates the direction of problem-solving activities within the manufacturing process.
Thanks to their knowledge and experience, our technicians can:
Set up rework campaigns on numerous products due to supplier shortages or quality-related issues with components. This could involve managing the entire process – from product identification through to repair and re-entry to the manufacturing process.
Rework non-conforming products to the required condition, as set out in a rework instruction sheet specifying the accepted criteria, and undertake secondary confirmation checks to ensure work conforms to specific standards.
Take completed products from the manufacturing process or sales compound that require retrofit or repair, replace or rectify the non-conformances to OEM quality/technical standards, and present ready for final buy-off by the OEM.
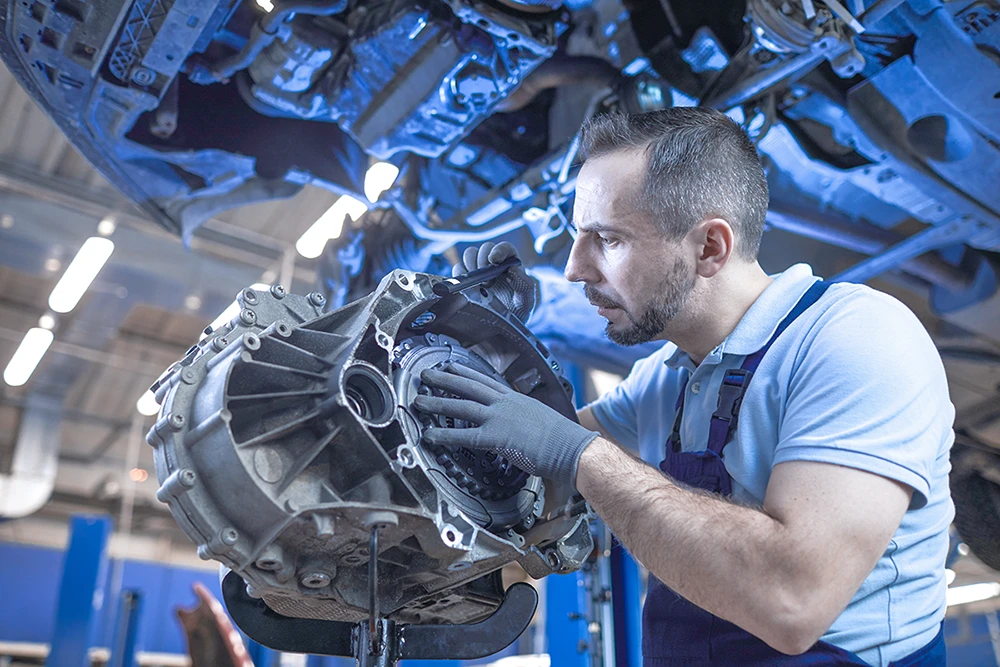
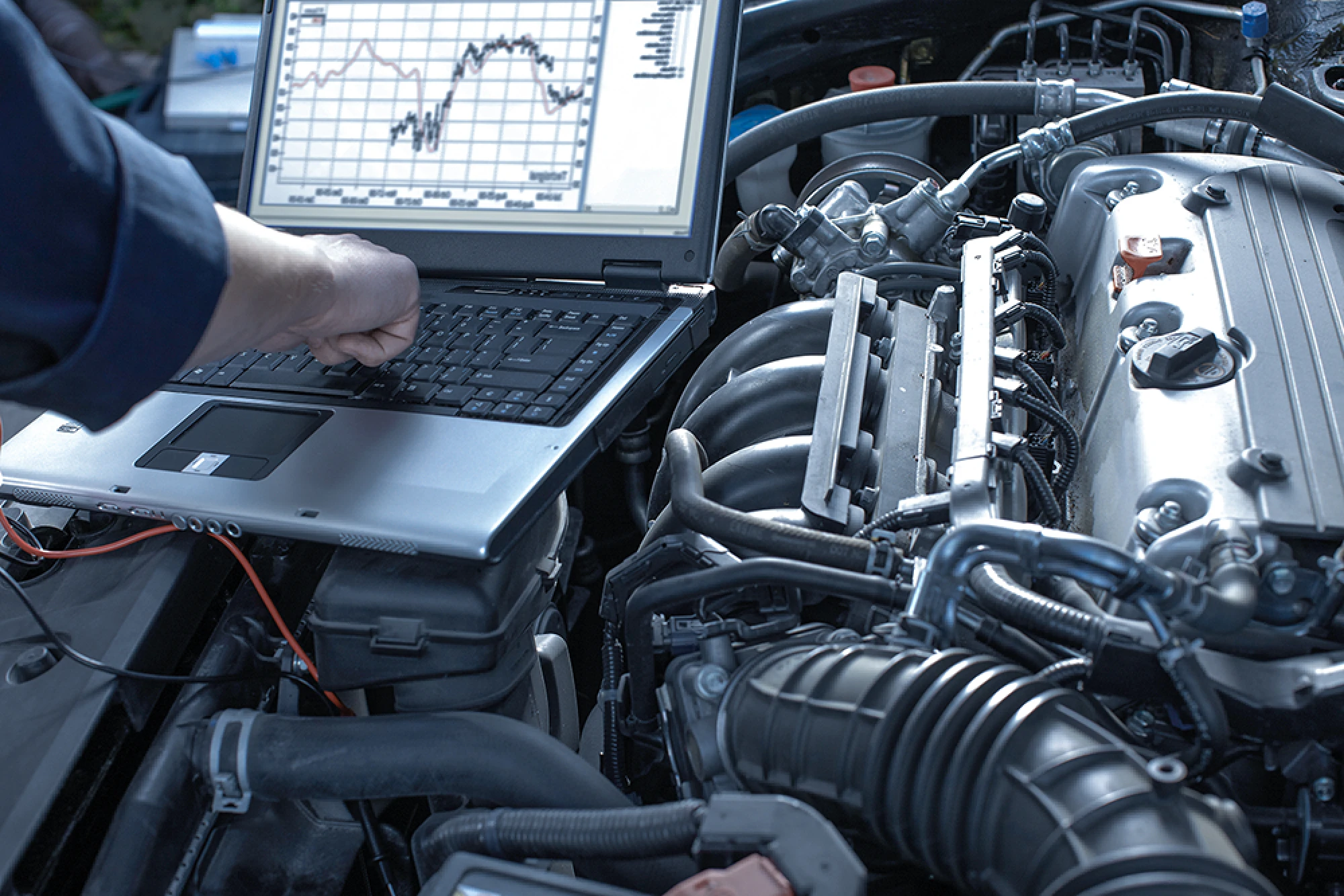
WIP Reduction
Our technicians can also be deployed to retrofit built products that cannot be currently sold due to quality issues. This helps to keep WIP levels down. Key capabilities include:
- Reading and recognising faults from a products build history record
- Fault finding and diagnosing fault causes on products
- Repairing products using formal repair instructions to the correct quality standards
- Testing and re-testing products pre/post repair
Reflash
Our technicians are skilled in reflashing software updates to completed products and individual components. They have extensive experience in using multiple techniques and tools, having been deployed on reflash exercises internationally.
All reflash activities are rigorously controlled and monitored to ensure that the correct software levels are uploaded.
GET IN TOUCH TODAY
Want to improve your business’s quality, efficiency & profitability?
G&P are an international service provider, enabling our clients to benefit from consistent service levels as well as localised points of contact.
Featured Case Study
Fast Turnaround – Speed without compromising quality
With a product launch imminent, an overseas automotive OEM urgently needed retrofit work on its new model to meet customer delivery deadlines. Without a rapid and efficient response, initial customer orders would be delayed causing profound reputational damage to the vehicle manufacturer.
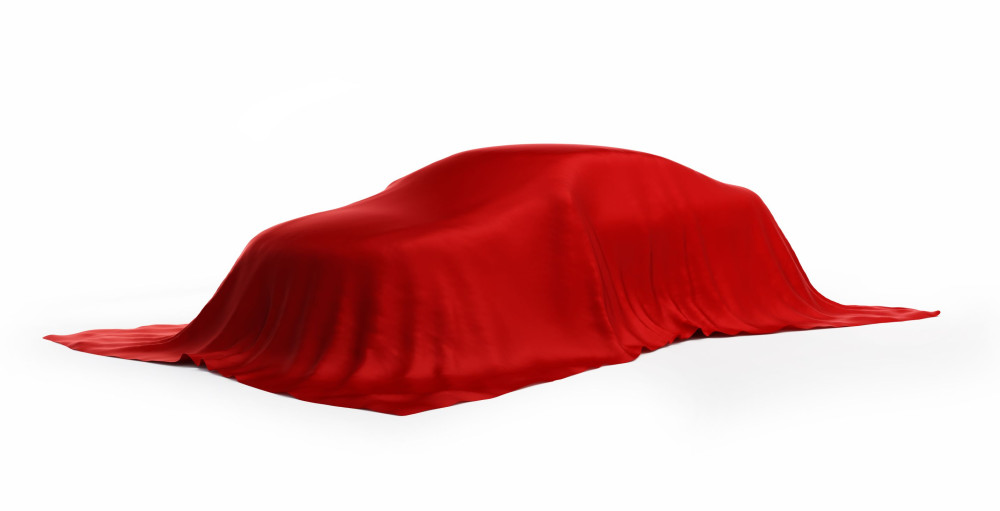