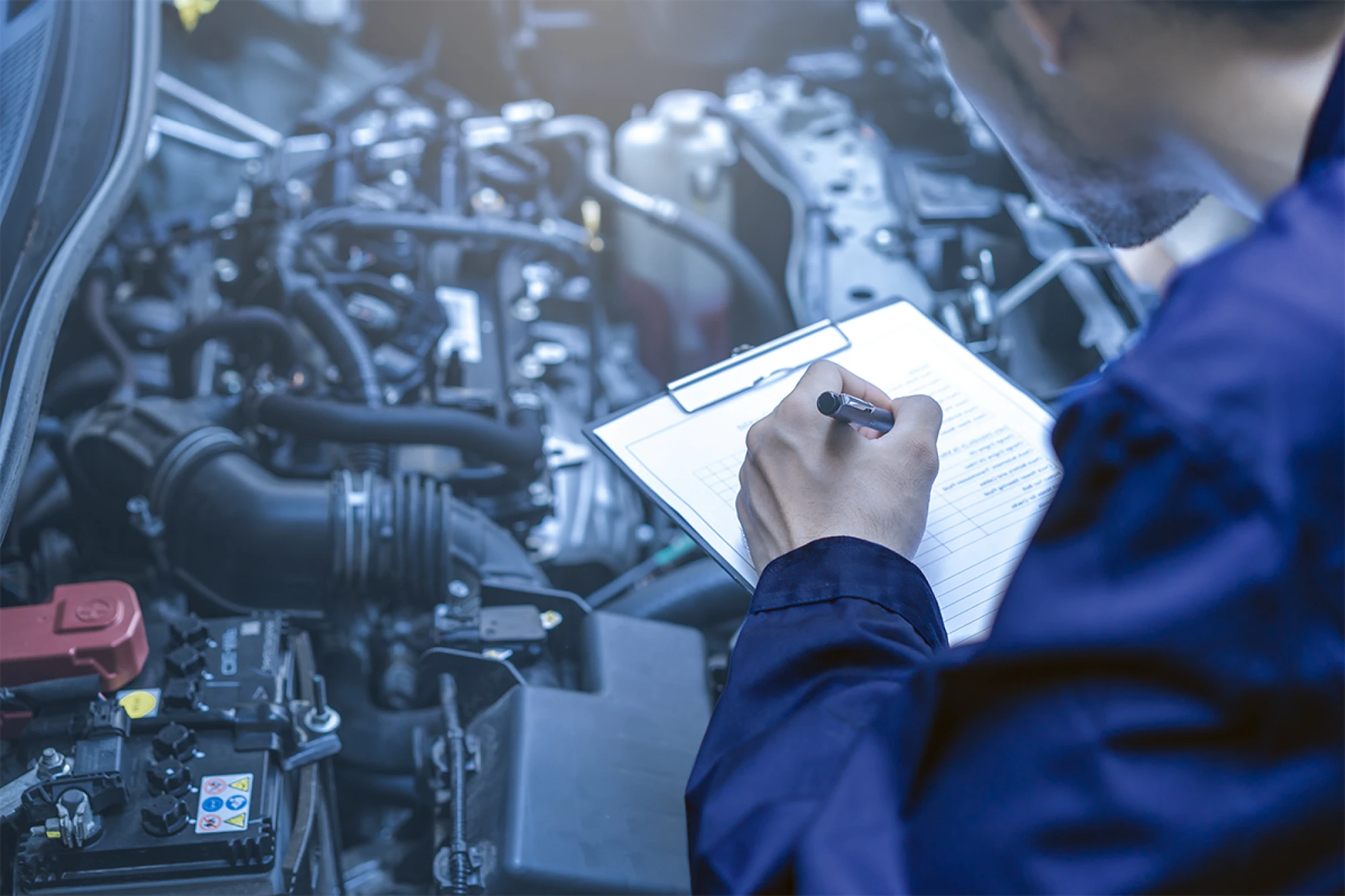
Technical
Final Product Audit
With more than 30 years’ experience operating at the global forefront of quality management, we can deliver independent, structured quality inspections of products at the end of the OEM manufacturing process to identify and contain quality issues. This prevents defects from leaving the plant and therefore helps to improve warranty performance and brand reputation.
Our final product acceptance process is a comprehensive audit covering all aspects of the product. Typically located on a moving line or conveyor (typically the customer acceptance or sales line), the audit is split across multiple stations to enable the logical division of audit criteria and the deployment of specialist technicians as required.
When a defect is detected, the product is diverted from being shipped and instead undergoes a comprehensive rectification process instead. Once repaired, the product will enter FPA again for a full recheck.
This process certifies that the original issues have been repaired and that no secondary issues have been created during the rectification process itself.

At G&P, we offer real time reporting and escalate issues as they are detected to prevent further similar defects from being created in the assembly process moving forward and supporting Customer Quality to work on solving any issues with the supplier of that particular component.
GET IN TOUCH TODAY
Want to improve your business’s quality, efficiency & profitability?
G&P are an international service provider, enabling our clients to benefit from consistent service levels as well as localised points of contact.
Featured Case Study
Vehicle Technicians – Seamlessly Integrated Within OEM’s Operations
One of the world’s leading OEMs wanted to protect and enhance its highly-sought after reputation, built over decades for producing vehicles that have become synonymous with its name.
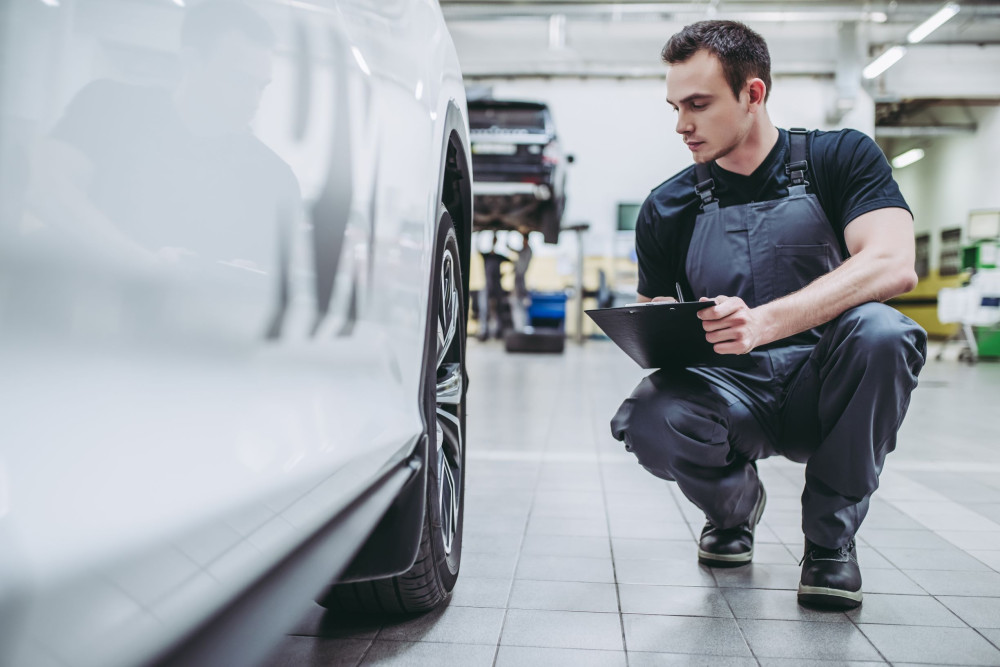