Supplier Performance Improvement – G&P Works With Industrial Engine Manufacturer To Manage Supplier Improvement Programme
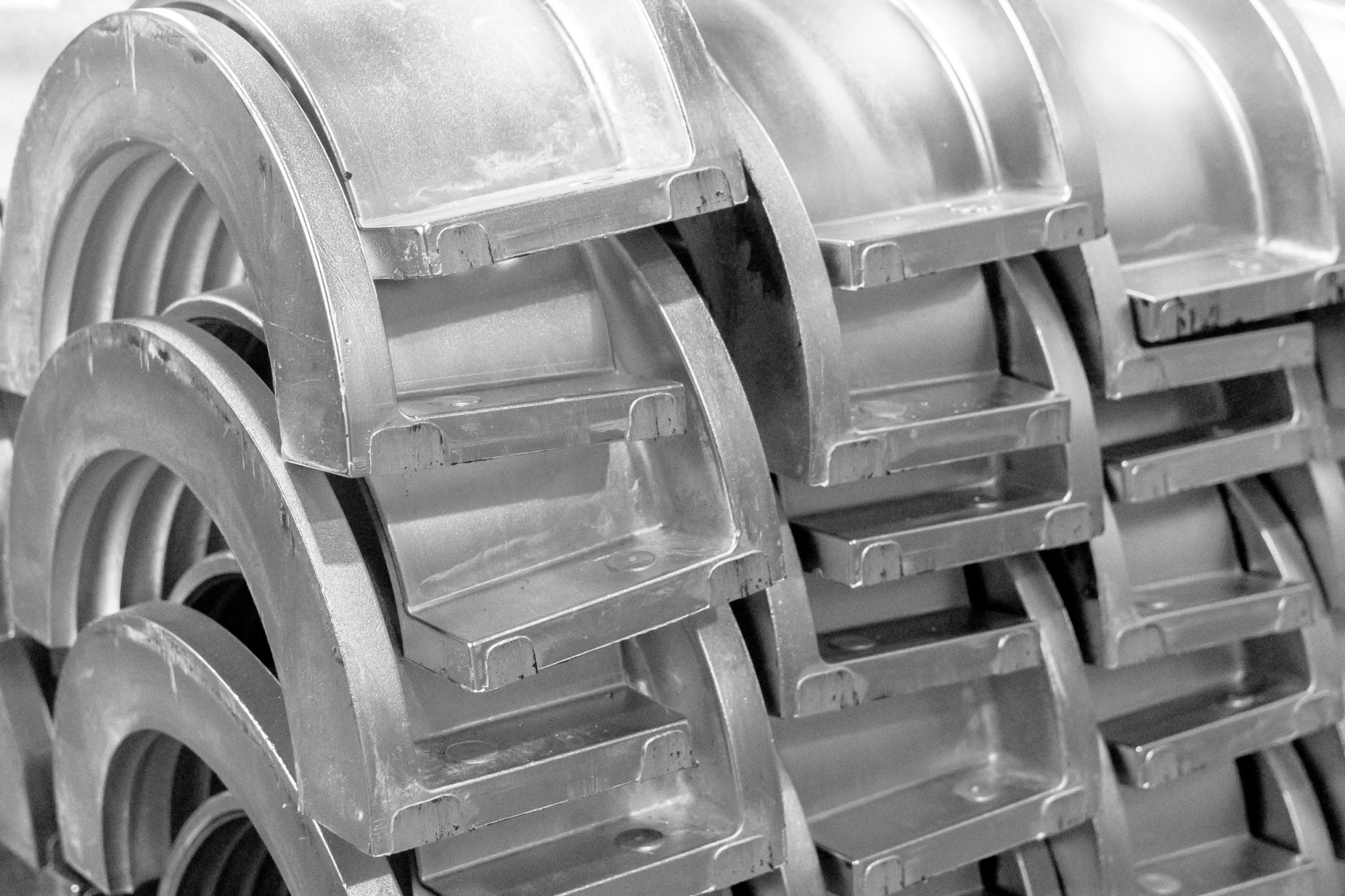
The Challenge
A global manufacturer of industrial engines with multiple production facilities across the UK, Europe, South America and Asia had identified a number of suppliers where performance was below expectations and was severely impacting production lines causing disruption and a loss of revenue.
One such supplier was highlighted as a significant risk due to consistent failure of their sub-tier supplier to deliver raw castings across multiple parts into their facility for machining. The significant arrears situation was further complicated by a design change requiring a stock-build on two of the constrained parts.
G&P were tasked with working with the supplier and their sub-tier supply chain to manage their recovery.
The Solution
G&P identified and allocated specialist supply chain performance engineers to support the supplier on behalf of our customer.
G&P's project team met the supplier team and discussed the steps at a kick-off meeting. The G&P engineers then conducted an in-depth analysis of both current and historical issues and developed mutually agreed action plans to resolve the supply issues as quickly as possible. The G&P team worked with the supplier and their sub-tier, developing pro-active working relationships to monitor the action plans and provide help where needed.
G&P’s team-working approach provided a conduit to effective communication, assisted with integration of improvement activities, provided focussed analysis of forward-view parts management by utlising bespoke trackers, all aimed at driving up schedule adherence.
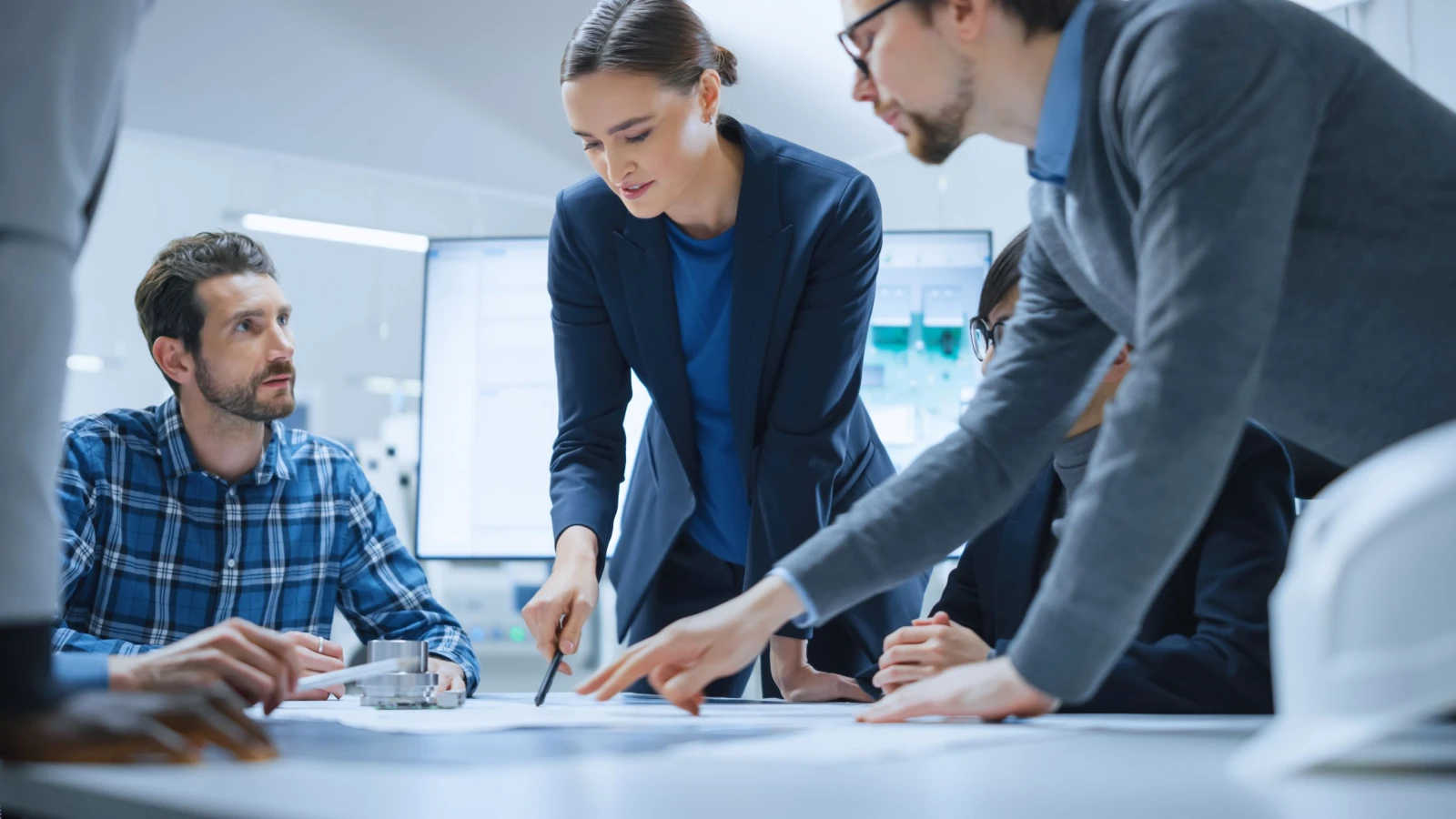
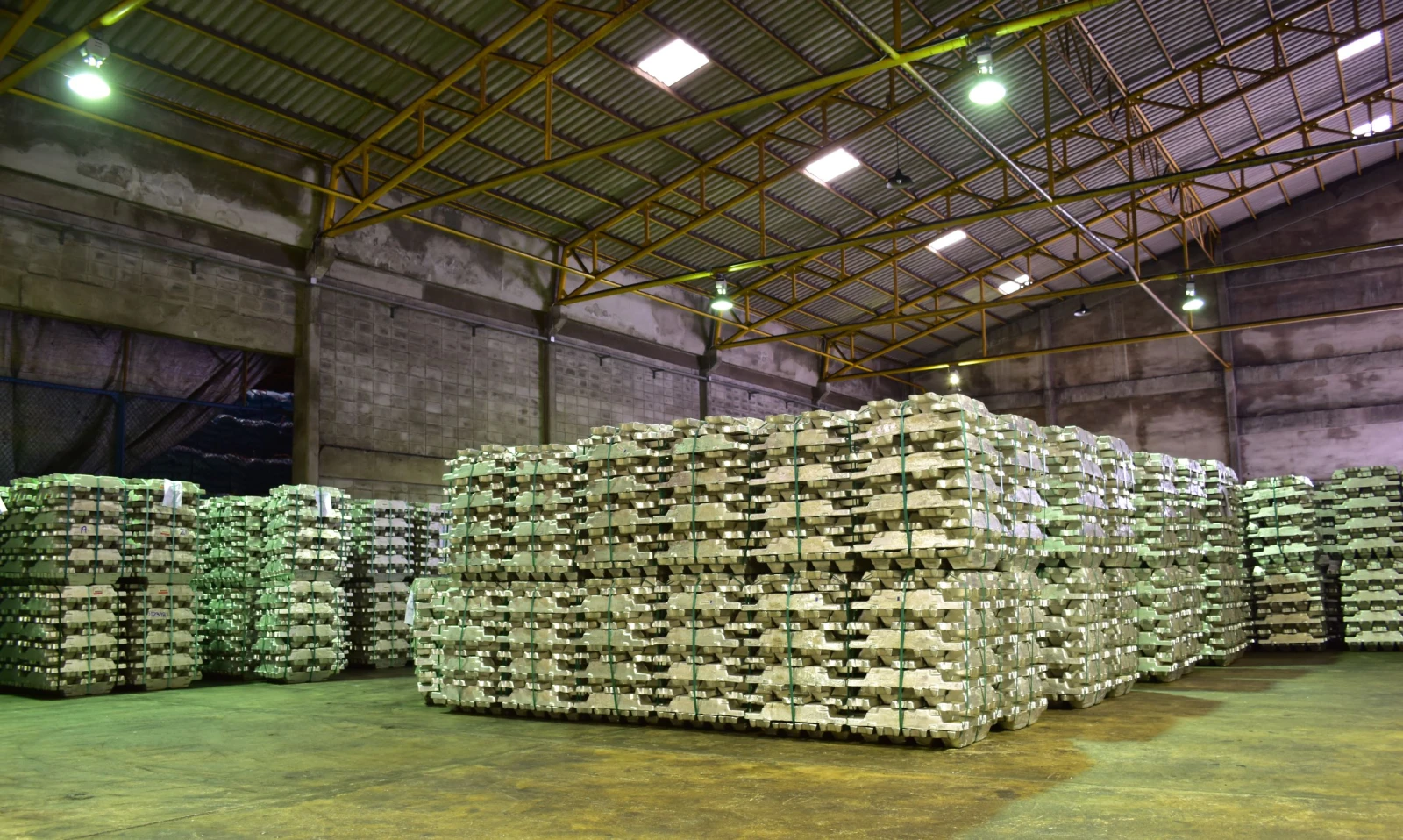
The Results
By prioritising critical path activities and daily feedback to our customer, the G&P team provided all-important confidence that supply of critical parts was secure and that the agreed improvement journey was being competently managed to the planned timings.
Additionally, G&P was further entrusted by the customer to support a NPI project team at this supplier, developing schedules and identifying sufficient stock levels of parts to facilitate engineering change with minimum disruption to production.
GET IN TOUCH TODAY
Want to improve your business’s quality, efficiency & profitability?
G&P are an international service provider, enabling our clients to benefit from consistent service levels as well as localised points of contact.